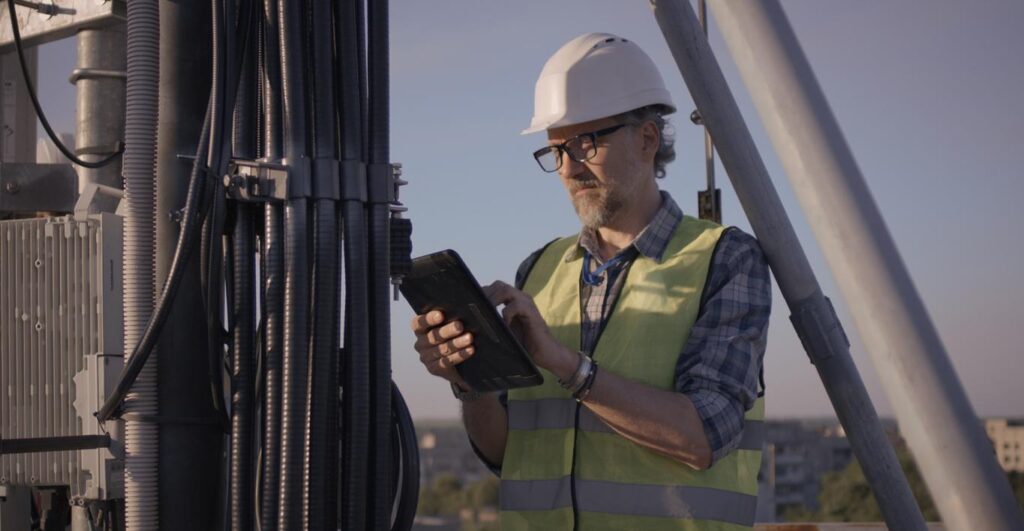
Getting OSP services right the first time
At the pace that telecom networks of all types, especially 5G multivendor networks, are being installed in urban, suburban, and rural areas, providers can’t afford to let technical issues slow these projects down. Communications Service Providers (CSPs) and their contractors have schedules and deadlines to meet, so the question is how to achieve the best and most reliable Outside-Plant (OSP) deployments and network installations on schedule and on budget? Making mistakes — and then having to fix them — slows everything down and increases costs. Quality Assurance and Quality Control (QA/QC) tools are critical to avoiding mistakes and delivering excellent networks. TrueNet Communications provides quality assurance, quality control, and state of the art tools, including TrueQ Pro, to support the best outcomes in OSP services.
Challenging construction issues with OSP services
Because telecom is growing rapidly to meet the huge demand for high-speed internet and 5G mobile data, the biggest challenges to OSP services are defects and re-work, leading directly to increased costs and schedule overruns. Especially now, with so many OSP network builds and a limited supply of experienced people, contractors are having to rely on a less experienced workforce, which shows in the final product.
Problems specific to OSP deployments include aerial installation defects from improper lashing and installation of components (such as cable, riser guards, down guys, and grounding) are common. So are underground installation defects from hardscape and softscape restoration, meeting the minimum fiber bend radius requirements, and proper installation of tracer wire systems.
It’s vital for a QA/QC program during OSP network deployment to ensure not only that a CSP gets the best network the first time, but that contractors (and the people they hire) understand the root causes of problems. TrueNet’s TrueQ Pro does that, and by partnering with contractors and subcontractors, it becomes a broad source of knowledge. That knowledge enables them to deliver the desired product faster, with less re-work.
TrueNet TrueQ Pro reduces re-work during OSP services
By establishing a three-way partnership with the provider and the contractors, TrueNet is in the best position to identify defects by acting as a coach and trainer to the OSP contractor. No contractor wants to perform re-work because it directly affects their bottom line. TrueNet identifies the most frequent re-work items and educates the contractors, limiting the number of return trips to a location. They deliver their client’s OSP deployment faster, the network is more reliable, and everyone is happier.
A typical approach to QA/QC in major 5G deployments
Most companies that don’t use a service like TrueNet typically have an in-house QA/QC team. This may be one or two people per market, covering multiple crews during peak construction. Unfortunately, that can leave a large portion of the network build unchecked. These in-house teams may be very knowledgeable, but typically the data isn’t quantified, and knowledge is simply lost when a team member leaves. Also, adherence to and application of specifications may not be standardized from market to market. Most importantly, these in-house teams rarely present information to their OSP contractor and subcontractors that might help educate them and deliver better results throughout the life cycle of the build. They may have a checklist, but they lack the time to check everything, and it’s basically a spot-check just to close out the job.
Creating a collaborative QA/QC approach that changes outcomes
A collaborative program that changes behavior is necessary for QA/QC. Then, the contractor doesn’t keep piling up the same mistakes as the build goes on. It can be more of a QA approach — observing the crews at work and providing ongoing feedback — or more of a QC approach — checking after the build and providing guidance for future work. But the QC approach doesn’t solve the immediate problem of costly re-work and remediation.
The TrueQ Pro program is unique in the industry
When the TrueQ Pro program was developed five years ago, TrueNet wanted to be sure it encompassed the entire lifecycle of a project in a way that is beneficial to both CSPs and contractors. All TrueNet inspections, photos, data, and checklists are in a database where network operators and contractors have access.
TrueNet can develop a national specification that also encompasses minor jurisdictional deviations, such as conduit depths in different areas or field condition deviations, as well as an analysis of all the defects found to determine critical network-affecting issues and safety concerns.
TrueQ is an amazing tool to educate contractors and subcontractors while minimizing their rework. When a subcontractor corrects any issues, they can upload photos for verification, which speeds up the process so that a segment of the project can be closed out more quickly. Both the network operator and contractor can see where any additional coaching or other changes are needed to move the project along and keep it on schedule.
Most QA/QC systems (many are just Excel-based or even paper-based) simply can’t handle the life cycle in the way TrueQ Pro can. They don’t have the dashboards that enable network operators and contractors to look at things quantitatively.
Speeding up OSP projects and minimizing rework
One example of efficiency with TrueNet TrueQ Pro compared to a traditional QA/QC process is during aerial inspections. By putting a GoPro on the end of a height stick, TrueNet can inspect five poles in the same time it takes to do one inspection with a bucket truck. The quality of the data provided, combined with the cost savings compared to the cost of using a bucket truck, is a truly compelling benefit. The information is received faster, plus it avoids the cost and hassle of the bucket truck and its operator, in addition to the traffic control costs and issues, to save at least 60% on inspection costs.
More about TrueNet OSP services
TrueNet Communications is a wholly owned subsidiary of Fujitsu Network Communications that provides professional services in the OSP market. This includes turnkey RAN deployment services and more. The TrueNet TrueQ Pro is a unique method for more effective 5G multivendor deployments that improves quality on current and future projects.