
Velocity and efficiency are key to maximizing the return on broadband infrastructure investments
In my previous blog in this Digital Infrastructure Investment blog series, I focused on risk. Now I turn my attention to Return On Investment (ROI) in broadband infrastructure projects. The first phase in the lifecycle is planning and network design, also known as Day 0. Day 1 is network construction, which includes operational readiness (network integration and commissioning, implementation of standard operating procedures, staff training, etc.) to make sure all systems are ready prior to going live. Finally, Day 2 is the operate and maintain phase when customers start using and paying for their broadband internet services. This is also when technical support and customer service kicks in, the customer base grows, and cash flow is generated to service availability payments. Getting from Day 0 to Day 2 is subscriber and revenue readiness and this is used to calculate the time-to-market required to launch a broadband business. A faster time-to-market means revenue can be realized sooner and a better ROI achieved.
In our experience, the two themes that have the most direct and significant impact on ROI are velocity and operational efficiency. Increasing velocity and efficiency require a focus across the business: the people, the processes, and the technology. In this blog, I examine these factors and some new ways they can be optimized to improve your overall broadband infrastructure project ROI.
Velocity
In 1748, Benjamin Franklin wrote, “remember that time is money.” For digital infrastructure projects, this means avoiding costly construction delays, securing first mover advantage in competitive markets, and implementing streamlined operational processes that can scale.
In-house or outsource?
Digital infrastructure investment projects require fully operational business readiness within two years from the initial financing commitment. Outsourcing is a way to build capabilities and capacity quickly in areas like HR, accounting, or customer service call centers. For Day 2 network operations, outsourcing is strongly recommended. The technical complexity of the network and the specialized skill sets required to maintain it are like that of a large operator, although on a smaller scale. Building up the expertise in-house takes time, which limits the ability to scale quickly. It’s also common to use a blended model with a small number of staff supported by an outsourced team to handle peak demand and/or to provide access to specialized technical experts. As the revenue and customer base grows, some functions can move in-house.
Leveraging digital twin technologies
During the Day 0 design phase, the Outside Plant (OSP) infrastructure (fiber conduits, poles, hubs, terminals) is specified. Optimizing the design and the CapEx requires accurate knowledge of the physical sites and routes, which is traditionally done with surveys and walkouts. OSP digital twin technology saves time by combining GIS mapping, LiDAR data, rights-of-way databases, and drone photography to create an accurate virtual model of the physical world.
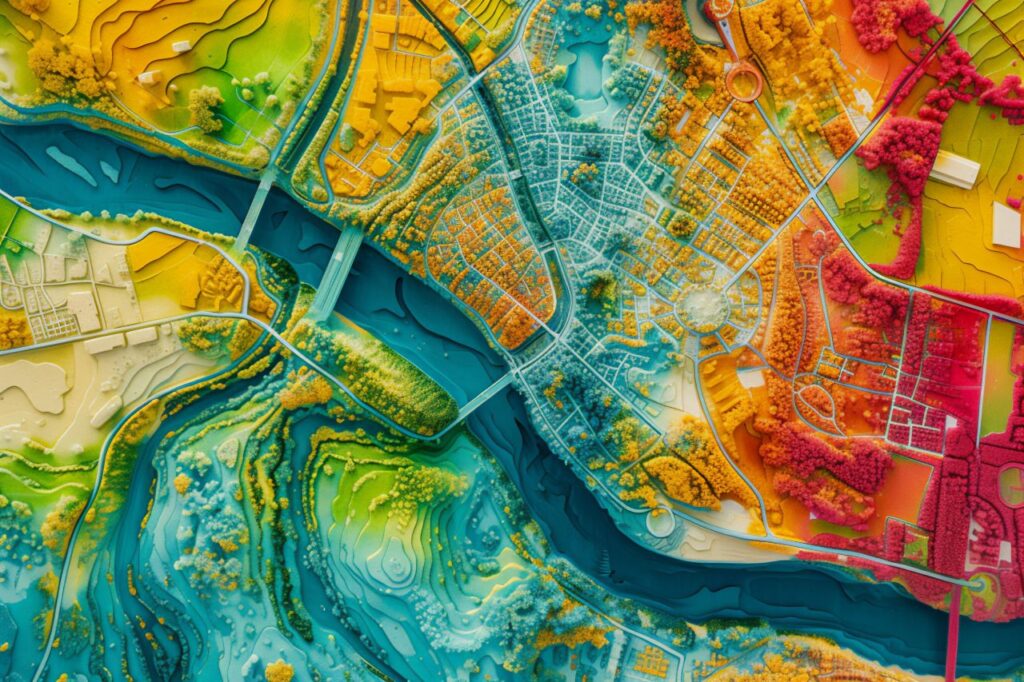
Instead of sending an engineer out to the field, OSP digital twins bring the field to the engineer. Avoiding truck rolls not only saves time but also enables easy scaling of remote design resources and specialists. Accelerating the network design and verification phase reduces the time-to-market.
Maintenance and troubleshooting benefit from digital twins as well. Predictive Artificial Intelligence/Machine Learning (AI/ML) algorithms look for signs of imminent equipment failure or sub-optimal operation and flag preventive maintenance measures. Logs and maintenance history, as-built diagrams, plus 3D views of every passive and active network element can be maintained in the database for access by field technicians. This information is also useful during service provisioning to ensure the correct fiber is connected to the correct port, both in the Inside Plant (ISP) and OSP network. This enhances the troubleshooting effort and time to resolution, but more importantly, service-disruption can be minimized by resolving imminent failures before they occur.
Managing schedules and hand-offs between phases and contractors
Utilizing a network systems integrator can give you a faster time-to-market. A network systems integrator has the experience to holistically approach network design. Equipment, software, and related systems (like OSS/BSS) are thoroughly tested together so that network efficiency and optimization can be realized. The integrator is also well positioned for complex project management that is accountable for managing multiple contractors and maintaining progress against the project schedule.
The importance of data integrity
One persistent issue that causes delays and headaches for many projects is data silos and management by spreadsheet. With numerous subcontractors and stakeholders involved from Day 0 through Day 2, there are multiple software platforms where information may be duplicated but not synchronized, and processes that are either poorly defined or weakly enforced. It’s a common problem that threatens to slow project execution.
An OSS/BSS system avoids reliance on siloed spreadsheets by centralizing end-customer profiles and physical locations with customer orders, billing, and provisioning. This functionality preserves data integrity and enables faster execution of tasks, such as adding new subscribers to a network. All-in-one platforms that combine customer order processing, billing, and service provisioning to streamline administrative tasks are available.
Centralized databases with vulnerable subscriber data are also easier to protect against cyber-security threats. As cyber-attacks increase in both frequency and sophistication, it is critical to design a robust security architecture from the start. Threat detection, threat response, and incident forensics should comply with industry standards and regulatory requirements.
Operational efficiency
Truck rolls consume some 48% of the total OpEx and is the single largest expense item, so this is a good place to look for savings.
People
Are all those field technician installations and service calls necessary? Self-service, self-install, and self-help options are becoming mainstream. A combination of clear processes and supporting software platforms can reduce the call volume. In one case, the field operations team believed 82% of support-related dispatched truck rolls were unnecessary. After a solution was implemented, the number unnecessary truck rolls dropped to 1%.
Outsourcing
The Network Operations Center (NOC) is the nerve center of any network. Building one from scratch, acquiring the necessary skills and operating procedures, and keeping it staffed 24x7x365 is an expensive undertaking. Outsourcing the NOC generally makes a lot of sense. Fujitsu offers managed NOC services with pricing based on subscriber size and growth, and our customers benefit from the economies of scale generated by a large operation. On average, 80% of trouble tickets are resolved remotely by the Fujitsu NOC.
Fujitsu’s full-service integration
With 3,600 North American infrastructure projects under our belt, Fujitsu has expertise in assessing, designing, building, operating, and maintaining fiber and wireless networks. Regardless of our role in your project (network systems integrator, fiber designer, outsourced NOC operator, or turnkey provider), we have proven services and solutions that can accelerate the ROI of your next broadband infrastructure project.